TR Electronics
TR Electronic is an industry leader in manufacturing and supporting position feedback, drive technology and sensor solutions world-wide. Through its complete line of absolute encoders, linear measurement systems and industrial sensors, TR Electronic is able to deliver exceptional results every time.
Rotary Encoders
TR-Electronic rotary encoders with optical or magnetic scanning precisely acquire position in steel production, wind power plants, cranes and ships as well as in explosion-proof versions in painting lines. Miniature versions ensure the correct position in medical technology and SIL3 approved absolute rotary encoders ensure the necessary safety.
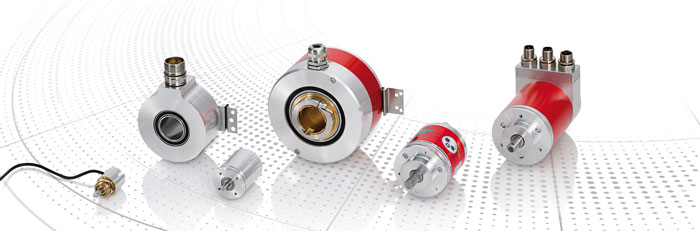
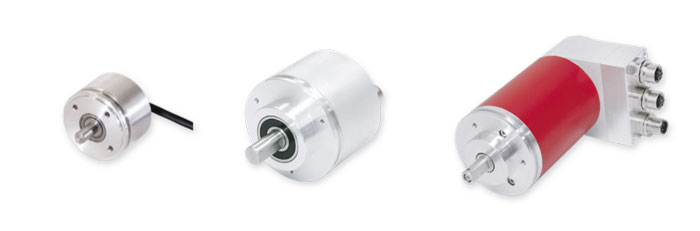
Absolute Rotary Encoder
The absolute rotary encoders in our product range are as varied as your individual requirements: From standard/compact rotary encoders with optical or magnetic scanning with solid shaft, hollow shaft, blind shaft or integrated coupling through SIL3/PLe certified safety encoders and absolute encoders with fully encapsulated electronics for outdoor applications, to double rotary encoders in different housing sizes and a multitude of interfaces.
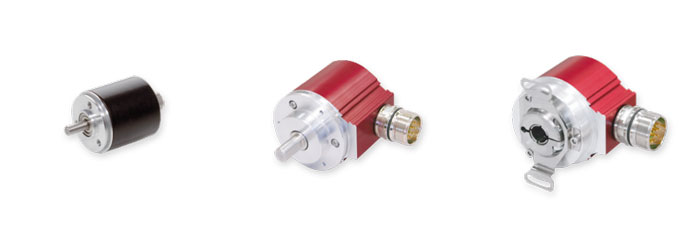
Incremental Rotary Encoder
Incremental rotary encoders are used in machines and installations in different resolutions. Thanks to their simple design, incremental rotary encoders are more economical to manufacture than absolute rotary encoders. On the other hand, they only indicate position changes and cannot detect movements without a power supply.
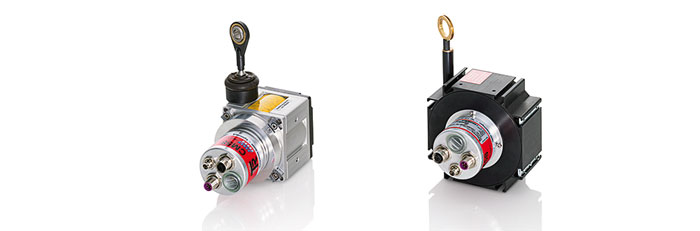
Wire-Actuated Encoder
Wire draw encoders by TR-Electronic are equipped with absolute or incremental rotary encoders and fit the specific encoder series perfectly.
Three classes fulfill specific needs for different mechanical loads, duty cycle, lifetime, resolution resp. reproducibility.
Linear Encoders
Linear absolute position measuring systems and position sensors (magnetostriction) measure linear movements e.g. in injection molding machines without contact and wear-free, or are integrated directly into hydraulic cylinders. Cascadable position sensors position parting units. High-resolution absolute position measuring systems with a glass scale ensure precise positioning on machine tools. And laser sensors based on phase difference measuring techniques position aisle stackers in the desired position extremely precisely in warehousing and materials handling technology.
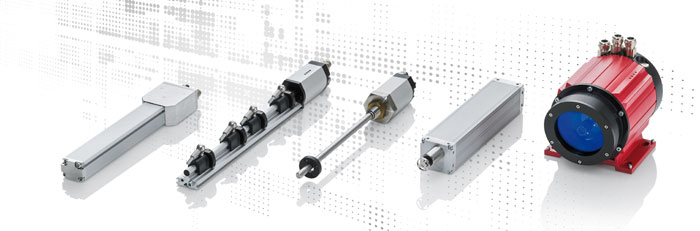
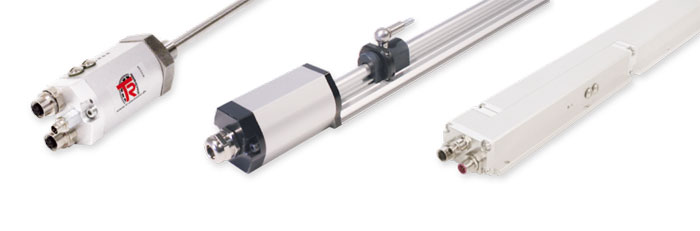
Magnetostrictive Linear Encoder
Linear absolute position measuring systems (magnetostriction) measure linear movements without contact and wear-free, even in aggressive media.
Pressure-resistant tubular housings made of stainless steel enable installation in hydraulic cylinders. You can also use versions with a separate external cladding tube to enable particularly easy changeover of the measuring system in hydraulic cylinders. We also offer linear encoders in a polypropylene housing for use in chemically aggressive media or for level measurement in the food processing and electroplating industries.
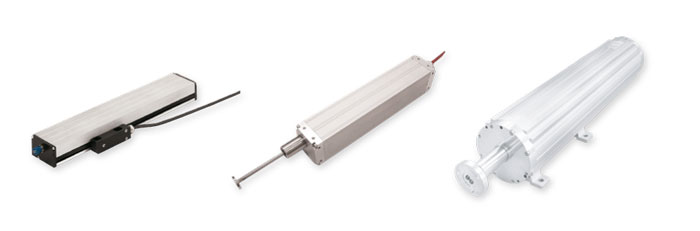
High-Resolution Position Sensors
High-resolution absolute position measuring systems with glass scale enable linear measurements in the µm range without time-consuming reference travel.
These absolute position sensors from TR-Electronic operate according to the principle of photoelectric scanning. With the smallest possible measuring step of 0,1 µm and a precision of ±5 μm, our systems are particularly well suited for applications which make high requirements on resolution and precision, and which also require an absolute measurement without reference travel.
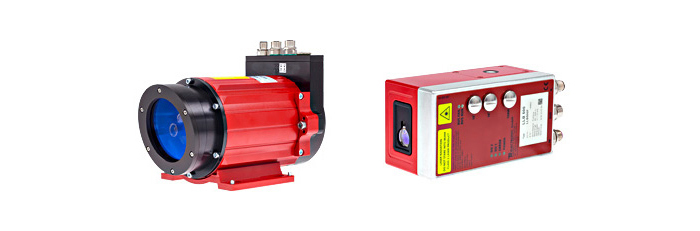
Laser Distance Measuring
Laser distance measuring systems from TR-Electronic are powerful optical sensors, which enable measurement of long distances without contact and fast enough for closed-loop control. The measuring system comprises a laser light source, light collector, electronic evaluation and data interface as well as a reflector.
Three classes fulfill specific needs for different mechanical loads, duty cycle, lifetime, resolution resp. reproducibility.
Power Gap - Inductive Power Supply and Signal Transmission
It is always difficult to install sensors and other devices in machines and equipment with rotating tables, moving pallets, tool changing and forming dies, because the equipment is restricted by fixed cabling. PowerGap meets customers' demands for wire-less solutions by inductively supplying power from a fixed part to a moving part and transmitting signals between the two.
Power Gap Advantages
- Cable - stress damage, limitation of physical movement, additional space requirements
- Connector - Wear and tear (maintenance is necessary), human error when connecting, protection requirement for exposed, connectors
- Slip Ring - Limited life cycle (maintenance is necessary), vulnerable to dust and liquids, increased size of rotary mechanism